الحار منتجات
ملكنا الإخبارية
shaft furnace iron ore pellet

Detailed Modeling of the Direct Reduction of Iron Ore in a Shaft
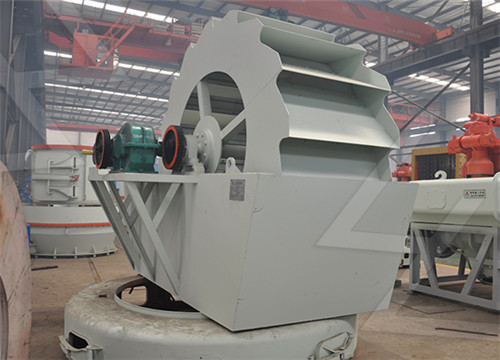
Direct Reduction of Iron Ore Pellets by Using CO/CO
2023/12/31 In a shaft furnace, the reducing gases injected into the middle and the bottom part of the shaft are gradually diluted by the spent gases emitted from the reduced pellets as it ascend upwards, which
获取价格
Mathematical Model of the Shaft Furnace for Reduction of Iron
Synopsis: A mathematical model of the shaft furnace is developed for gaseous reduction of iron-ore pellet. In the model, the reduction of iron-oxide is defined as the multi-stage
获取价格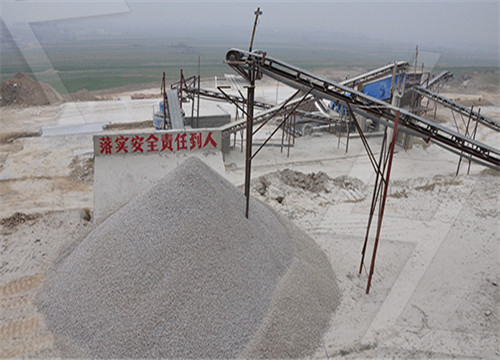
Reduction of Iron Ore Pellets, Sinter, and Lump Ore
2020/3/23 A blast furnace (BF) is the dominant process for making iron in the world. ... Herein, the reducibility of the iron ore pellet, sinter, and lump ore in the BF shaft are focused on. The experiments are
获取价格
Optimization of the Iron Ore Direct Reduction Process
2018/6/27 The shaft furnace is the core of the DR process. Iron ore pellets are charged at the top, descend due to gravity, and encounter an upward counter-flow of gas. The reducing gas (CO and H 2, plus CH 4,
获取价格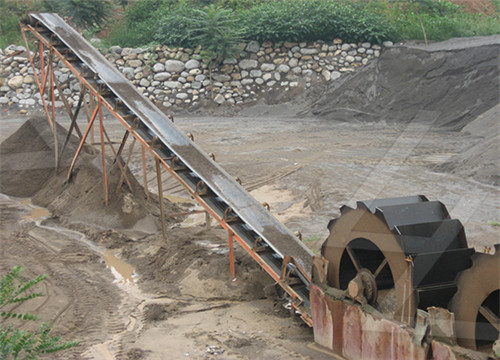
Swelling behavior of iron ore pellet reduced by H2–CO mixtures
2015/1/1 1. Introduction. Volume swelling of iron ore pellets accompanied with strength decrease appears commonly during reduction. In order to ensure permeability
获取价格
Iron ore pellet disintegration mechanism in simulated shaft
2017/7/15 The disintegration behavior and mechanism of iron ore pellet in simulated shaft furnace conditions were investigated in details. Effects of temperature, reducing
获取价格
Iron ore pellet disintegration mechanism in simulated shaft
2017/4/1 Abstract. The disintegration behavior and mechanism of iron ore pellet in simulated shaft furnace conditions were investigated in details. Effects of temperature,
获取价格
Iron ore pellet disintegration mechanism in simulated shaft
DOI: 10.1016/J.POWTEC.2017.04.056 Corpus ID: 100586641; Iron ore pellet disintegration mechanism in simulated shaft furnace conditions @article{Yi2017IronOP, title={Iron ore
获取价格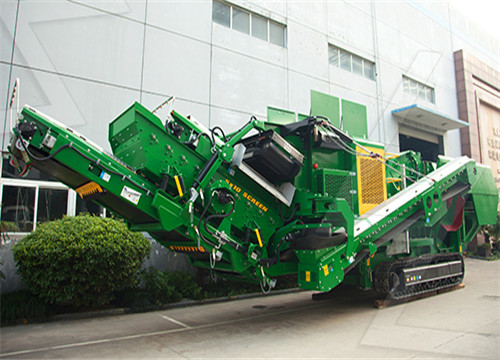
Mathematical model of direct reduction shaft furnace and its ...
1986/1/1 By using this model, the influence of the different conditions of reducing gas on the reduction of iron oxides has been examined. Further, experiments were conducted on the reduction of iron ore pellets with the use of a small shaft furnace having an inside diameter of 0.25 m and a reduction zone height of 2.7 m.
获取价格
Modeling and Simulation of the MIDREX Shaft Furnace ... - Springer
2015/8/21 The direct reduction is a process for reducing iron ore and producing sponge. There are several technologies, like MIDREX1 and H.Y.L2 using the countercurrent shaft furnace to make sponge iron.. In MIDREX technology, the furnace is a vertical shaft (Fig. 1).A charge of pelletized or lump ore is loaded into the top of the furnace and
获取价格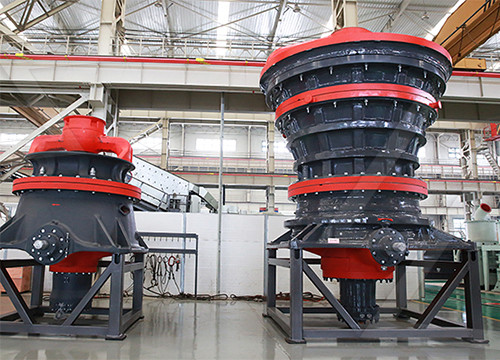
MODELING THE IRON ORE PELLETS REDUCTION ON
2015/12/1 The process for pelletizing iron ore fines is an important operation unit for producing high quality of raw materials for the subsequent reduction processes such as blast furnace or direct reduction.
获取价格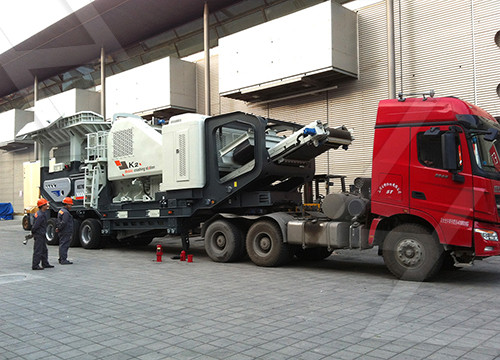
Global green hydrogen-based steel opportunities surrounding
2023/5/4 The shaft furnace operates using a counterflowing ore and reducing gas to produce a sponge iron product, requiring ore in pellet form with minimum 67% Fe content 21 to limit ore impurities and ...
获取价格
Sticking behaviour and mechanism of iron ore pellets in COREX
2019/2/1 COREX is a clean process releasing lower pollution and consuming fewer cokes than the blast furnace process. However, serious sticking phenomenon often occurs in COREX shaft furnace, causing many problems to the normal operation. In this study, the loading reduction experiments of iron ore pellets were carried out under the simulating
获取价格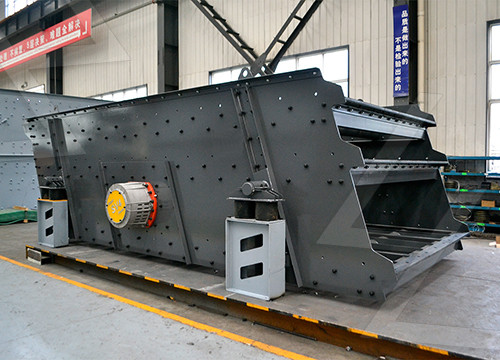
Adapting to Raw Materials Challenges: Part 1 - Midrex Technologies, Inc.
General pellet chemistry – The type and percentages of chemical elements will determine the tendency of pellets to stick and form clusters in the shaft furnace. Process upset conditions in the shaft furnace can result in significant iron unit loss to non-prime product, which may or may not be suitable for recycling through the shaft furnace.
获取价格
Direct reduced iron process - tec-science
2018/6/21 Figure: Shaft furnace for the direct reduced iron process. The heart of the direct reduction is the shaft furnace, which is filled from the top with lump ore and pellets. Carbon monoxide and hydrogen are used to dissolve out the oxygen in the iron ores. In contrast to the blast furnace process, however, these reduction gases do not
获取价格
Iron ore pelletization - ScienceDirect
2015/1/1 Iron ore pellets are essential burden materials to improve the performance of modern blast furnaces, because they possess high iron grade, low silica and alumina contents, excellent mechanical strength, and metallurgical performance with a uniform size distribution. ... and rotation speed of the damp mill. Damp milling is widely used in shaft ...
获取价格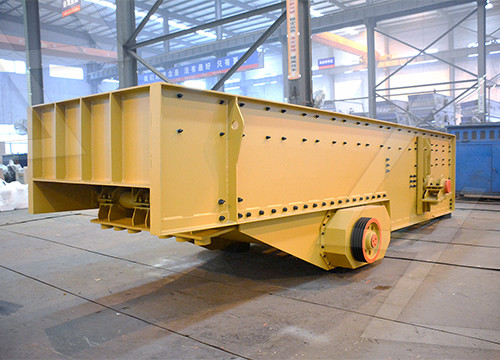
Detailed Modeling of the Direct Reduction of Iron Ore in a Shaft Furnace
2018/10/1 This paper addresses the modeling of the iron ore direct reduction process, a process likely to reduce CO2 emissions from the steel industry. The shaft furnace is divided into three sections (reduction, transition, and cooling), and the model is two-dimensional (cylindrical geometry for the upper sections and conical geometry for
获取价格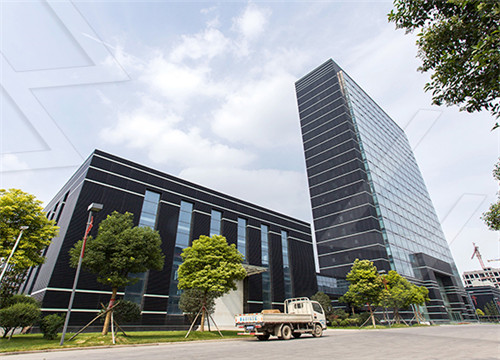
DR-Grade Iron Ore Pellets - Midrex Technologies, Inc.
Total iron ore pellet production and sales by the Swedish company were 24.6 and 22.9 million tons, respectively, in 2017. This compares with 2016 production and sales of 24.0 and 22.7 million tons, respectively. ... Blast furnace pellets made up 55% of sales value and DR pellets accounted for 26%. According to iron ore trade statistics, Sweden ...
获取价格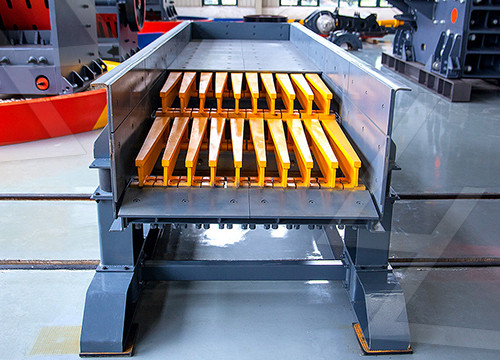
Iron Ore Pelletizing Process: An Overview IntechOpen
2018/7/11 In 1943, E. W. Davies and co-workers demonstrated the process using an experimental shaft furnace. Commercial operation started in the 1950s in Sweden using vertical-shaft-kilns for firing the pellets. ... Souza R, Mendonca C, Kater T. Production of acid iron ore pellet for direct reduction using an organic binder. Mining Engineering.
获取价格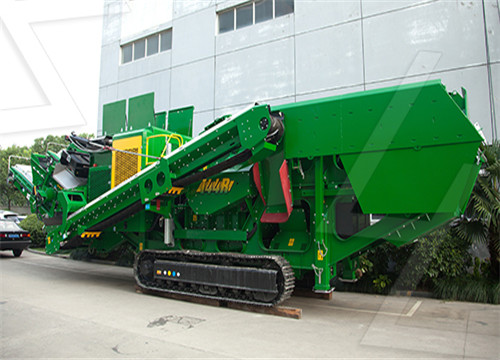
Effect of titanium on the sticking of pellets based on hydrogen ...
2024/2/17 Direct reduction based on hydrogen metallurgical gas-based shaft furnace is a promising technology for the efficient and low-carbon smelting of vanadium–titanium magnetite. However, in this process, the sticking of pellets occurs due to the aggregation of metallic iron between the contact surfaces of adjacent pellets and has a serious
获取价格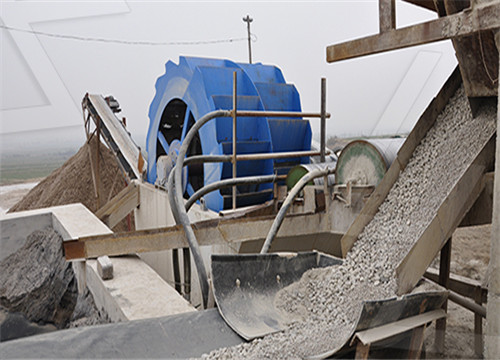
The MIDREX® Process
In the early days of direct reduction, there was a clearly discernible difference between iron oxide pellets intended for blast furnace use (BF-grade pellets) and those used to make DRI to feed an EAF. A “DR-grade” pellet typically has higher iron content and less silica, alumina and other gangue constituents than “BF-grade” pellets.
获取价格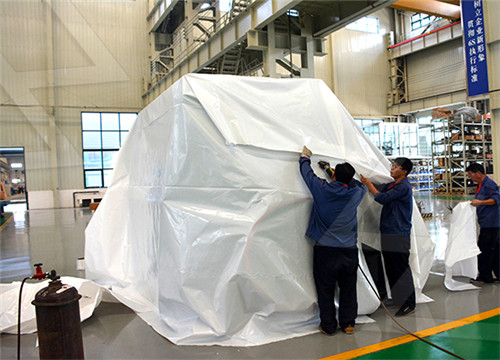
Iron ore pellet disintegration mechanism in simulated shaft furnace ...
2017/7/15 The disintegration behavior and mechanism of iron ore pellet in simulated shaft furnace conditions were investigated in details. Effects of temperature, reducing gas and gangue compositions were emphatically discussed. It was found that pellet disintegrated acutely as reduced by H 2 /CO = 0.8 at 550 °C. Gangue minerals in pellet
获取价格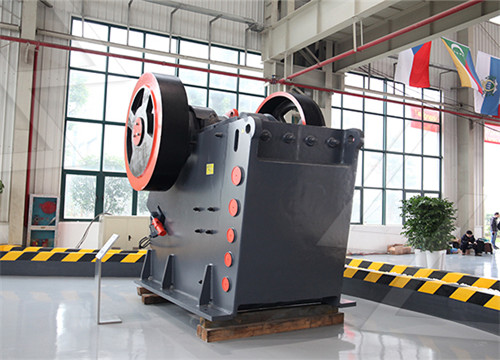
Iron Ore Pelletizing Process: An Overview IntechOpen
2018/7/11 In 1943, E. W. Davies and co-workers demonstrated the process using an experimental shaft furnace. Commercial operation started in the 1950s in Sweden using vertical-shaft-kilns for firing the pellets. ...
获取价格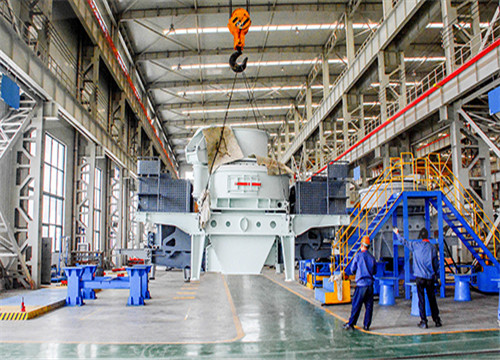
Effect of titanium on the sticking of pellets based on hydrogen ...
2024/2/17 Direct reduction based on hydrogen metallurgical gas-based shaft furnace is a promising technology for the efficient and low-carbon smelting of vanadium–titanium magnetite. However, in this process, the sticking of pellets occurs due to the aggregation of metallic iron between the contact surfaces of adjacent pellets and has a serious
获取价格
The MIDREX® Process
In the early days of direct reduction, there was a clearly discernible difference between iron oxide pellets intended for blast furnace use (BF-grade pellets) and those used to make DRI to feed an EAF. A “DR-grade” pellet typically has higher iron content and less silica, alumina and other gangue constituents than “BF-grade” pellets.
获取价格
Iron ore pellet disintegration mechanism in simulated shaft furnace ...
2017/7/15 The disintegration behavior and mechanism of iron ore pellet in simulated shaft furnace conditions were investigated in details. Effects of temperature, reducing gas and gangue compositions were emphatically discussed. It was found that pellet disintegrated acutely as reduced by H 2 /CO = 0.8 at 550 °C. Gangue minerals in pellet
获取价格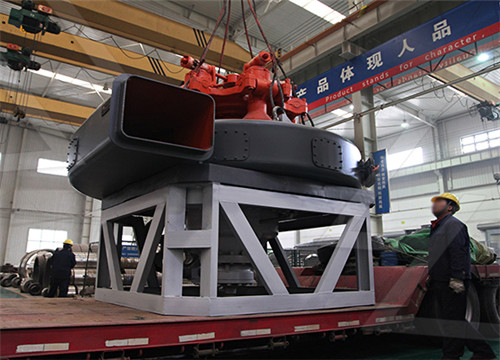
Reduction of Iron Ore Pellets, Sinter, and Lump Ore under
2020/3/23 A blast furnace (BF) is the dominant process for making iron in the world. ... Herein, the reducibility of the iron ore pellet, sinter, and lump ore in the BF shaft are focused on. The experiments are conducted isothermally with a blast furnace simulator (BFS) high-temperature furnace at four different temperatures (700, 800, 900, and 1000
获取价格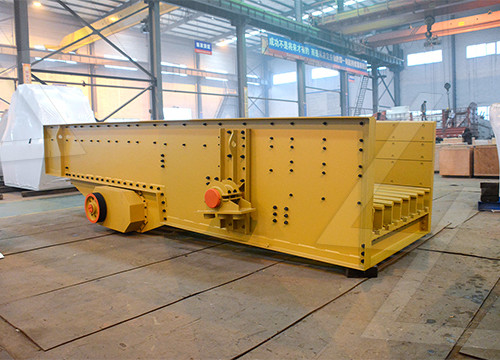
Iron Ore Pellets: North America, BF and DR Grade, Supply
3rd COREM Symposium on Iron Ore Pelletizing Sept. 29 – Oct. 2, 2013 Quebec City . BF Grade Pellet Supply NAFTA . NAFTA Blast Furnace Pellet Balance 2012 ... shaft furnaces: pellets, lump ore key physical properties are size consist, mechanical strength: economic importance
获取价格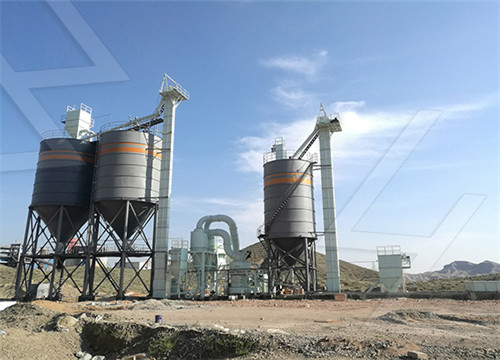
Direct Reduced Iron: Most Efficient Technologies for Greenhouse ...
2019/7/19 Iron ore, in pellet or lump form or both, is introduced to the MIDREX reduction shaft. As the iron ore descends through the furnace, the reformed reducing gas reacts with the Fe 2 O 3 in the iron ore and converts it to DRI, leaving H 2 O and CO 2 as off-gas (Kolbeinsen 2010).
获取价格
DRI production International Iron Metallics Association
Direct reduction of iron is the removal of oxygen from iron ore or other iron bearing materials in the solid state, i.e. without melting, as in the blast furnace. The reducing agents are carbon monoxide and hydrogen, coming from reformed natural gas, syngas or coal. Iron ore is used mostly in pellet and/or lumpy form.
获取价格
Process modelling for the production of hydrogen-based direct
2024/5/22 This process modelling study explored the behaviour of hydrogen-based direct reduced iron (DRI) manufacturing in a shaft furnace. Various performance parameters such as metallisation ratio (MR), consumption of hydrogen per tonne of DRI, production of by-products, reactor energy demand and total energy demands for the
获取价格
Coating of iron oxide pellets for direct reduction
2002/6/1 Depending upon their chemical composition and, to a lesser extent, on their physical properties, iron oxide pellets exhibit varying degrees of sticking tendency during direct reduction at elevated temperatures. For an efficient shaft furnace operation in direct reduction (DR), it is imperative to prevent pellets from sticking to each other and, hence,
获取价格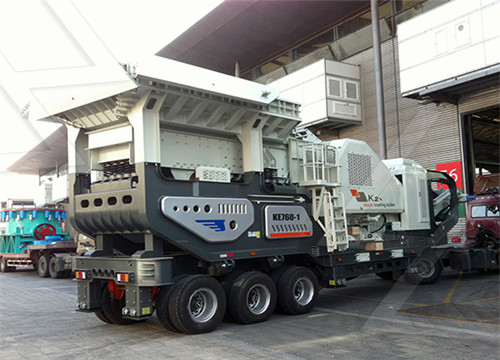
Sticking in Shaft Furnace and Fluidized Bed Ironmaking ... - Springer
2024/7/26 Shaft Furnace. For pellet sticking, the factors can be categorized into three main groups: (a) ore characteristics, (b) induration conditions, and (c) reduction conditions. The chemistry and mineralogy of iron ore pellets can have a significant effect on their sticking behavior during reduction.
获取价格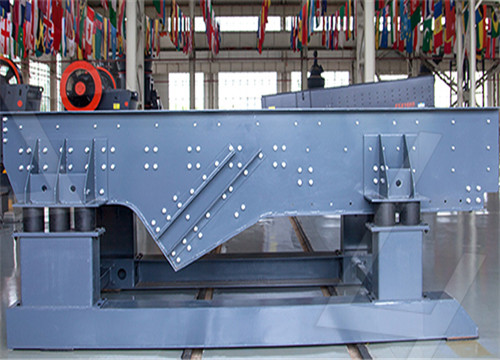
Sticking behaviour and mechanism of iron ore pellets in
2017/8/10 In this study, the loading reduction experiments of iron ore pellets were carried out under the simulating COREX reducing conditions. The influence of temperature and H 2 content in the syngas on the sticking behaviour of the pellets was observed by scanning electron microscope, energy-dispersive spectrometer and X-ray diffraction. The
获取价格
Modeling and Simulation of the MIDREX Shaft Furnace
2015/8/21 parts of the MIDREX reduction furnace including a solid–gas countercurrent moving bed reactor, tran-sition and cooling zones. In this system, iron ore pellets are reduced by the use of CO and H 2 as reducing gases and then they pass the transition Fig. 1. Shaft furnace of MIDREX process (adapted from Ref. 3). 2682 Shams
获取价格
Iron Ore Pellet - an overview ScienceDirect Topics
Fluidized bed DR processes are exceptions. Shaft furnaces use pellets (produced in the same way as pellets for the BF), or lump ore. ... The composite pellets [73–75] are being developed to use wood char fines for producing reduced iron ore pellets in a rotary hearth furnace. The added wood char would act as a reductant while the heat energy ...
获取价格مطحنة متناهية الصغر مطحنة فائقة النحافة للبيع
معدات التعدين محطم خام الذهب
مزدوجة كسارة الأسطوانة المورد من مصر
التحقيق في تأثير محطم
مطاحن عمر بن عمر ولاية قالمة
مُصنع سحق الدولوميت في الأردن
شركة ريموند للمطاحن السعودية
الحجر الجيري سحق الشركة في الهند
الهيكلية كسارة الفك
كسارة صخور صغيرة تعمل باليد صغيرة
شاشة لغسل الحصى البازلاء
new zealand gold screening plant
كسارة الحجر الفك العمل تحميل الفيديو
مطحنة سحرية طحن الحجارة
سعر آلة مطحنة التعدين في الهند
تستخدم الحجر كسارة
كيف uxite التعدين تؤثر على البيئة
المحاجر نيوزيلندا الجديد والتعدين
شبكة الاتصالات العالمية الفك محطم
يوتيوب تشكيل معادن
الشركات المصنعة الألمانية من معدات التعدين في جنوب أفريقيا
كسارات معروضه للبيع
عملية تعدين ركاز الحديد ومعدات تعدين ركاز الحديد
الطلب الكلي في نيجيريا
يستخدم مصنع غسيل الذهب الحجر
كسارات مخروطية مستعمل Nz
حول لدينا
تأسست شركة Henan Lrate للعلوم والتكنولوجيا المحدودة التي تصنع معدات التكسير والطحن الكبيرة والمتوسطة الحجم في عام 1987. وهي شركة مساهمة حديثة مع البحث والتصنيع والمبيعات معًا.
على مدار أكثر من 30 عامًا ، تلتزم شركتنا بنظام الإدارة العلمية الحديث والتصنيع الدقيق والريادة والابتكار. الآن أصبحت LIMING رائدة في صناعة تصنيع الآلات المحلية والخارجية.