الحار منتجات
ملكنا الإخبارية
cement industry finish grinding process
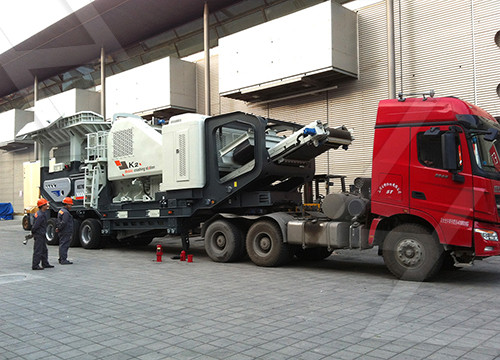
An overview of energy savings measures for cement industries
2013/3/1 Energy-efficiency measures for finish grinding in cement industry. This section describes measures to improve energy efficiency for the finish grinding
获取价格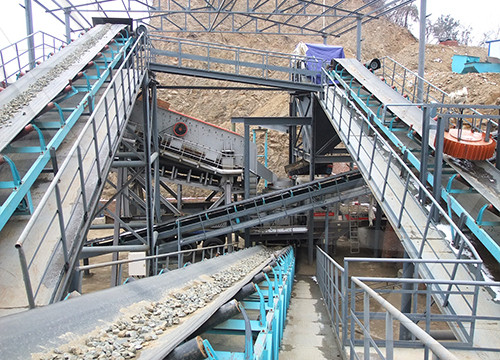
Cement Finish Milling (Part 1: Introduction History) - LinkedIn
2019/12/2 The finish mill system in cement manufacturing is the second to last major stage in the process, where the feed material is reduced in size from as large as several
获取价格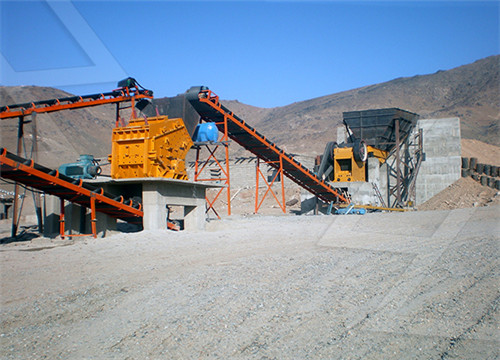
Grinding process optimization - IEEE Xplore
2017/6/19 As a world-wide leader in grinding solutions for the cement industry and understanding the changing needs of cement producers and how to tailor solutions to
获取价格
Energy-Efficient Technologies in Cement Grinding IntechOpen
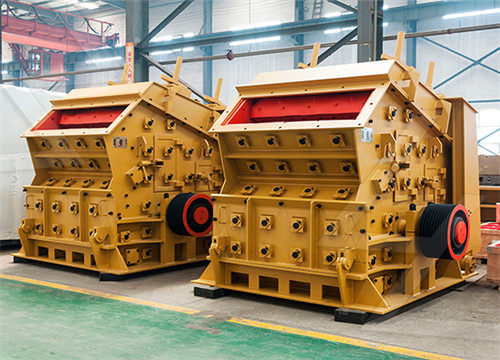
[PDF] Energy-Efficient Technologies in Cement
2016/10/5 In this chapter an introduction of widely applied energy-efficient grinding technologies in cement grinding and description of the operating principles of the related equip‐ ments and comparisons over
获取价格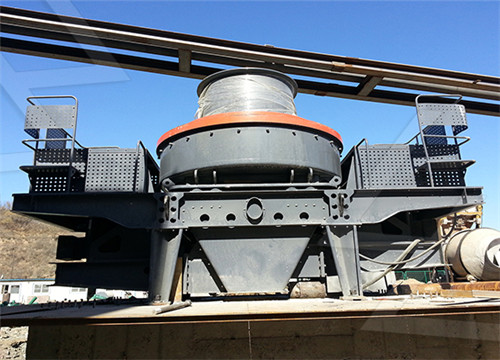
Cement Grinding - 911 Metallurgist
2016/10/22 A typical raw mix consists of 75-85% limestone, 12-25% shale, the balance consisting of silica or quartzite and iron oxide. Exact proportioning is dependent upon their chemical properties before and
获取价格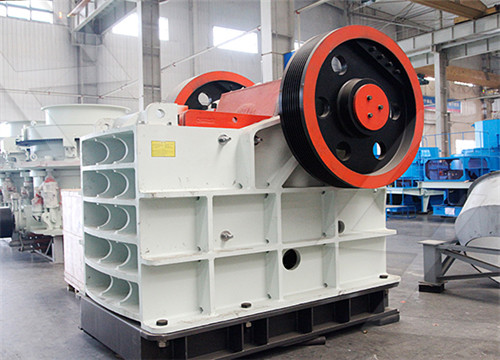
CEMENT GRINDING SYSTEMS - INFINITY FOR CEMENT EQUIPMENT
The final manufacturing stage at a cement plant is the grinding of cement clinker from the kiln, mixed with 4-5% gypsum and possible additives, into the final product, cement . In a
获取价格
Finish grinding: an overview of recent advancements and options
1995/6/9 Cement milling has traditionally been considered more art than science. In the last 10 years, significant improvements in process equipment have been made and
获取价格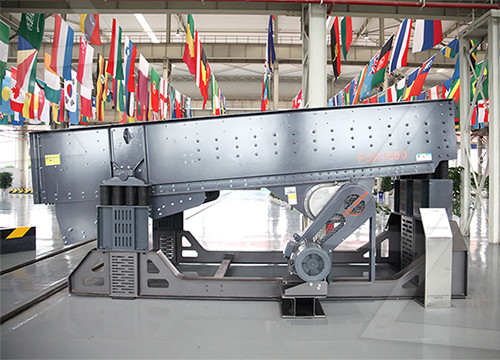
Energy efficiency of cement finish grinding in a dry batch ball mill
2006/3/1 In the cement industry, the clinker grinding step consumes about one-third of the power required to produce one ton of cement. This refers to an average specific
获取价格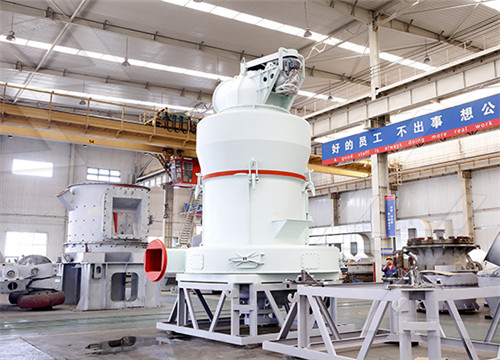
Cement Grinding Unit Process High Quality
At the Cement Grinding Stage, 90 – 95% of the clinker is mixed with gypsum and ground in a Cement Ball Mill to produce quality cement OPC 43 and OPC 53. In case of PPC Cement, there is an addition of Fly Ash.
获取价格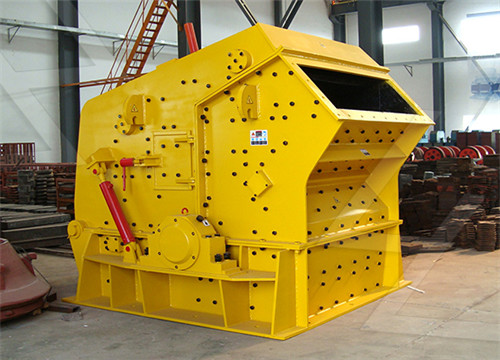
[PDF] Energy-Efficient Technologies in Cement
2016/10/5 In this chapter an introduction of widely applied energy-efficient grinding technologies in cement grinding and description of the operating principles of the related equip‐ ments and comparisons over
获取价格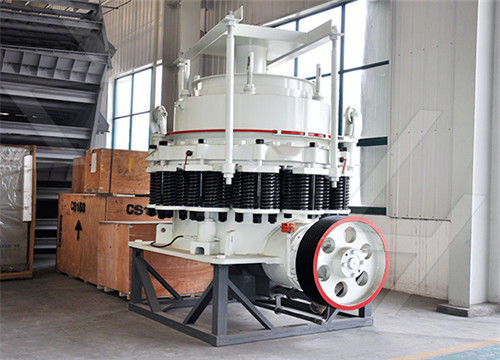
How Is Cement Produced in Cement Plants Cement
The laboratory of a cement plant. With the help of vertical roller mills or other types of crushers, the raw materials are blended and further ground into smaller pieces of raw meal in the cement plant. In a roller mill, the
获取价格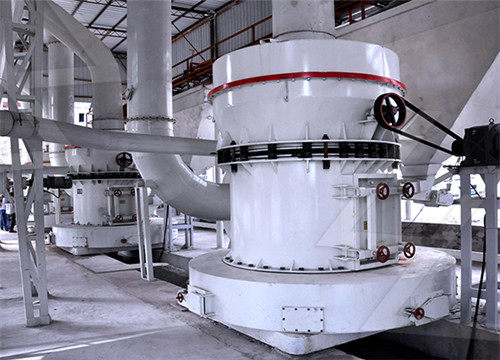
11.6 Portland Cement Manufacturing - US EPA
1971/8/17 to the process during the finish grinding operations described below. These materials, also excavated from quarries or mines, are generally purchased from an external source, rather than obtained directly from a captive operation by the cement plant. The portland cement manufacturing industry is relying
获取价格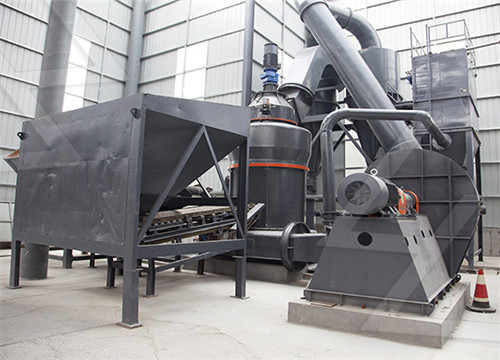
Clinker grinding technology in cement manufacturing
2019/1/3 Clinker grinding technology is the most energy-intensive process in cement manufacturing. Traditionally, it was treated as "low on technology" and "high on energy" as grinding circuits use more than 60 per cent of total energy consumed and account for most of the manufacturing cost. Since the increasing energy cost started
获取价格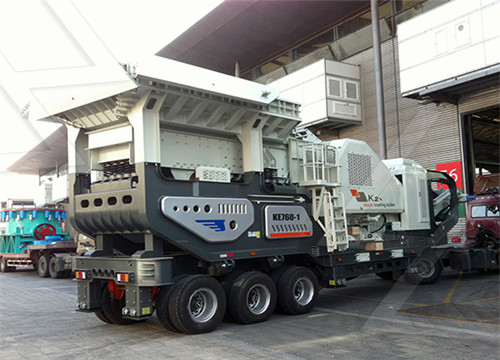
Grinding Solutions - Indian Cement Review
2015/1/31 From hub-and-spoke model to split grinding; from single-grinding solution to a combination of system solutions; and from energy-intensive traditional ball mill to upgraded versions and use of pre-grinders, the cement industry is shifting towards more energy-efficient grinding solutions. ICR trains its spotlight on the current technology
获取价格
An overview of energy savings measures for cement industries
2013/3/1 Energy-efficiency measures for finish grinding in cement industry. This section describes measures to improve energy efficiency for the finish grinding process in cement plants. 5.1. Process control and management in grinding mills for finish grinding. To achieve good quality products, control systems regulate the flow in the mill and
获取价格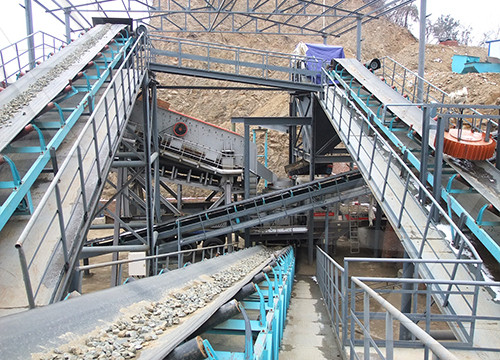
Energy and cement quality optimization of a cement grinding circuit ...
2018/7/1 Comminution in cement manufacturing takes place in both raw meal and finish grinding operations and responsible for about 60% of the whole electrical energy utilization [2], [3], ... International Process Engineering in the Cement Industry, Bauverlag GmbH – Wiesbaden and Berlin, 1985. Google Scholar [35] S. Strasser, R.A. Somani,
获取价格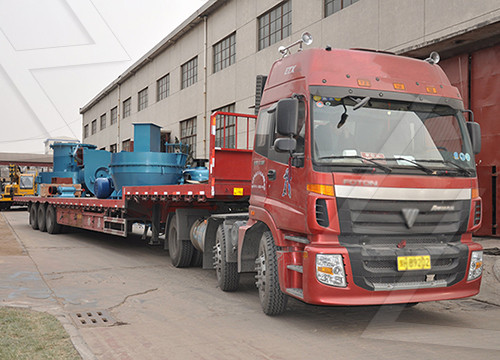
11.6 Portland Cement Manufacturing - U.S. Environmental
the process during the finish grinding operations described below. These materials, also excavated from quarries or mines, are generally purchased from an external source, rather than obtained directly from a ... Five different processes are used in the portland cement industry to accomplish the pyroprocessing step: the wet process, the dry ...
获取价格
Cement Manufacturing Process Engineering Intro
2012/8/30 Roller crushes the material to a fine powder and finishes the job. Raw mix is stored in a pre-homogenization pile after grinding raw mix to fine powder. Cement Manufacturing Process Phase III: Pre-heating Raw Material. After final grinding, the material is ready to face the pre-heating chamber.
获取价格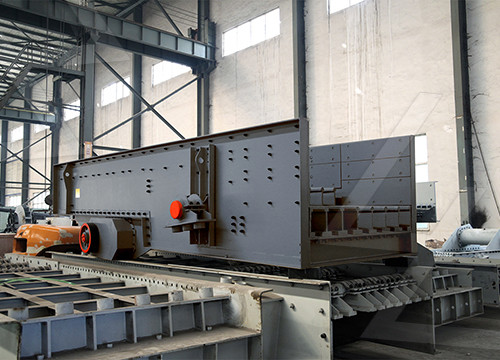
Everything you need to know about clinker/cement Grinding
Kurt B. thinks that flash dryer internals are not used in the cement industry, despite what is shown in the books. Rotary Dryer / Flash Dryer Comparision ... Ball and liner coating can occur in raw as well as finish grinding. Ball coating can be a result of the following conditions: ... cement mill, dry process raw mill, wet process raw mill ...
获取价格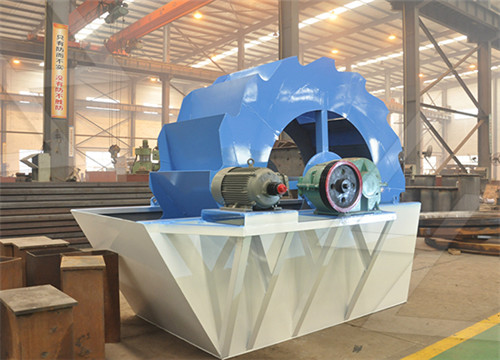
Cement Finish Milling (Part 1: Introduction History) - LinkedIn
2019/12/2 The finish mill system in cement manufacturing is the second to last major stage in the process, where the feed material is reduced in size from as large as several centimeters in diameter, down ...
获取价格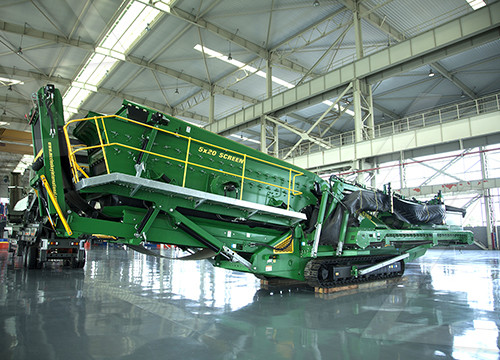
How Cement is Made - Portland Cement Association
Some manufacturers grind the raw materials dry, while others use a wet-grinding process involving water. Quarrying. Cement manufacturers quarry raw materials including limestone, clay, and sand. ... The cement and concrete industry is dedicated to reaching carbon neutrality by 2050 or sooner. The use of lower-carbon cement blends, alternative ...
获取价格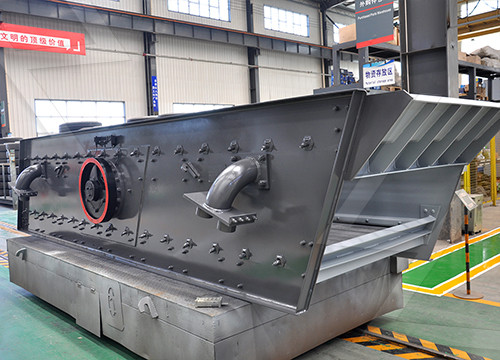
Grinding - Corrosionpedia
2024/7/19 Grinding is a subset of cutting, as grinding is a true metal-cutting process. Grinding is very common in mineral processing plants and the cement industry. Grinding is used to finish workpieces that must show high surface quality and high accuracy of shape and dimension. It has some roughing applications in which grinding
获取价格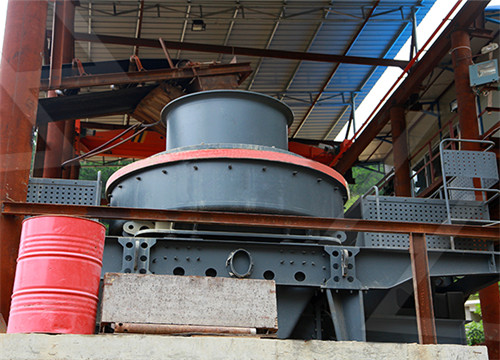
Everything you need to know about clinker/cement
Kurt B. thinks that flash dryer internals are not used in the cement industry, despite what is shown in the books. Rotary Dryer / Flash Dryer Comparision ... Ball and liner coating can occur in raw as well as finish grinding. Ball
获取价格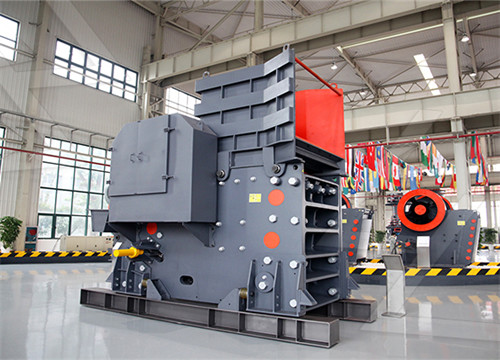
Cement Finish Milling (Part 1: Introduction History) - LinkedIn
2019/12/2 The finish mill system in cement manufacturing is the second to last major stage in the process, where the feed material is reduced in size from as large as several centimeters in diameter, down ...
获取价格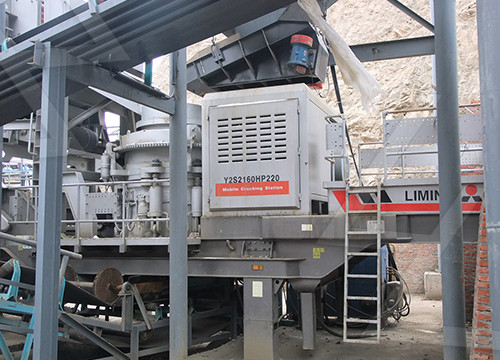
How Cement is Made - Portland Cement Association
Some manufacturers grind the raw materials dry, while others use a wet-grinding process involving water. Quarrying. Cement manufacturers quarry raw materials including limestone, clay, and sand. ... The cement
获取价格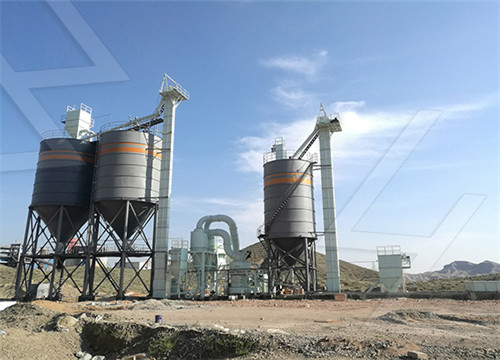
Grinding - Corrosionpedia
2024/7/19 Grinding is a subset of cutting, as grinding is a true metal-cutting process. Grinding is very common in mineral processing plants and the cement industry. Grinding is used to finish workpieces that must show high surface quality and high accuracy of shape and dimension. It has some roughing applications in which grinding
获取价格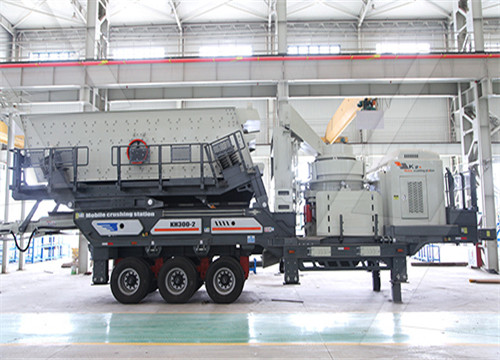
The Cement Plant Operations Handbook - International
Providing a comprehensive guide to the entire cement production process from raw material ... the industry’s favourite technical reference book is now fully updated with new material and an extended chapter on alternative fuels. Key sections covering ... Cement milling Finish milling is the grinding together of clinker with some 3-5 per cent ...
获取价格
The Cement Production Process
Calcining and burning or clinkering — the conversion process that takes place within the cement kiln and associated equipment. Finish milling — the grinding of clinker to produce cement. Raw Materials. The main raw material for the manufacture of clinker is a lime-bearing material.
获取价格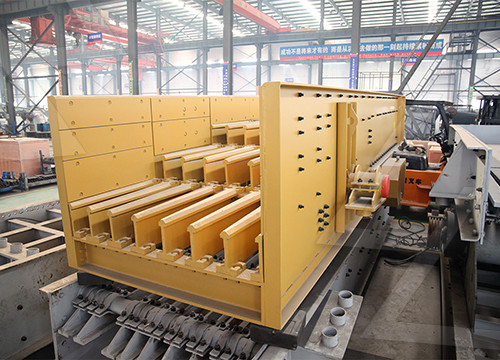
Application of sustainable techniques in grinding process
2024/3/11 Grinding is a machining process that entails the meticulous removal of material from a workpiece through the utilization of abrasive grains [].This method, executed by grinding machines, is pivotal for achieving stringent tolerances, refining surface finishes, and sculpting specific shapes or profiles [].Abrasive materials like aluminium oxide,
获取价格
Process technology for efficient and sustainable cement production ...
2015/12/1 The reason for the very limited additional potential savings of thermal energy is the necessary heat for the clinker production process. Fig. 1 shows the heat flows, the thermal input, the use for clinkering and drying, and the remaining waste heat flows that might be utilised. However, the remaining waste heat is already used to a high degree,
获取价格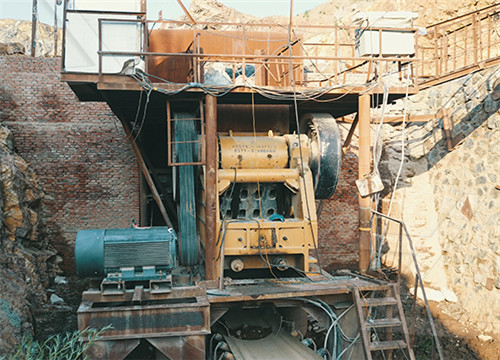
Cement Manufacturing Process - INFINITY FOR CEMENT EQUIPMENT
There is a lot of crusher used in cement industry such as; Impact crusher; Hammer crusher; Jaw crusher; ... The process is called a drying /grinding process, where most of the material/product is transported pneumatically by drying gases. ... Reduced clinker porosity can make the clinker harder to grind, increasing finish mill power consumption ...
获取价格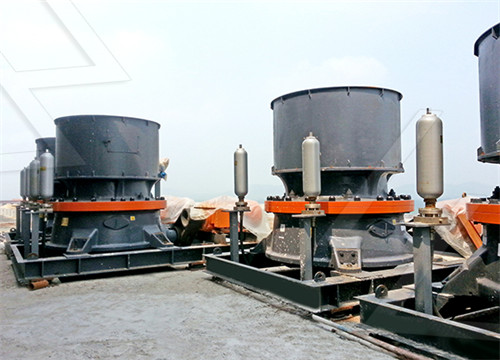
Concrete Grinding, Honing and Polishing - The Basics
2021/4/19 A polished concrete surface has clarity of reflection like a mirror and has a glass-like finish. The Variables. The process of grinding, honing, and polishing concrete is more technical than most ...
获取价格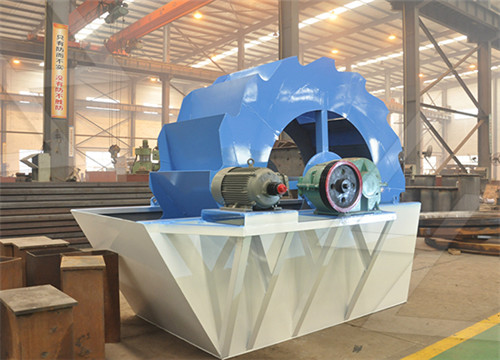
Energy efficiency of cement finish grinding in a dry batch ball mill
2006/3/1 In the cement industry, the clinker grinding step consumes about one-third of the power required to produce one ton of cement. This refers to an average specific power consumption of 57 kWh per ton [1]. Such large amounts of energy justify the need to improve the energy efficiency of comminution process.
获取价格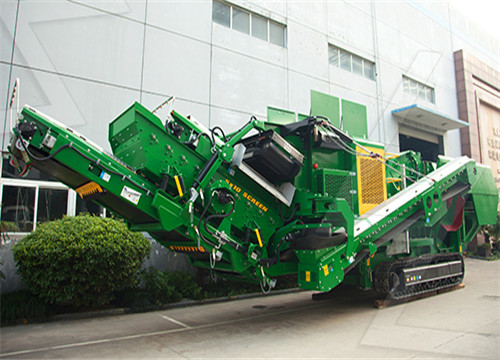
PROCESS CONTROL FOR CEMENT GRINDING IN VERTICAL ROLLER MILL
The power ingesting of a grinding process is 50-60% in the cement production power consumption. The Vertical Roller Mill (VRM) reduces the power consumption for cement grinding approximately 30-40% associated with other grinding mills. The process variables in cement grinding process using VRM are strongly nonlinear and having
获取价格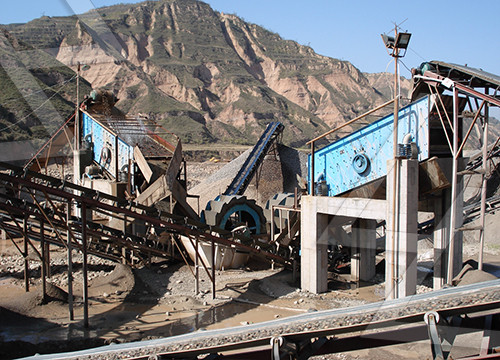
Industrial application of large raw material roller press finish ... - ZKG
This paper introduces the large raw material roller press finish grinding system developed by Tianjin Cement Industry Design Research Institute Ltd, which adopts newly developed equipment and process technology, such as the large raw meal roller press, new combined separator, low-resistance and high-efficiency cyclone, high-efficiency fan, and intelligent
获取价格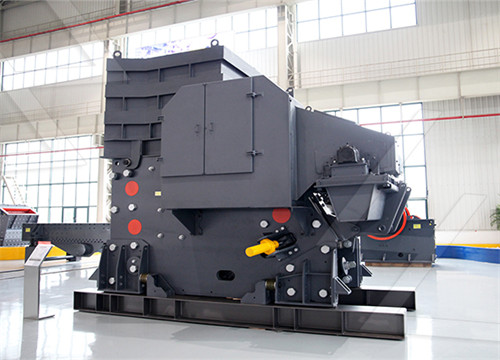
Finish grinding - INFINITY FOR CEMENT EQUIPMENT
Finish grinding . The finish grinding process is one of the basic tech nical operations of cement production as well as the concluding process. The manner in which this opera tion is conducted, determines the quality of the cement. ... When grinding cement, the additive must also have been shown not to be harmful to the finished cement.
获取价格نانو كربونات الكالسيوم طحن النبات
آلات مطاحن الدقيق الهند
معدات التكسير في الولايات المتحدة
معدات التعدين للبيع في وادي ترابوكو
مطحنة الكرة لمعالجة الرخام كسارة المحاجر
تمثيل تصويري لمطحنة المطرقة
آلات التعدين مطحنة الألغام
كيفية تصنيع الكروم في طحن الكرات
إزالة الغبار الكسارات
مطلوب محجر الحجر في ولاية كيرالا
موقع تعدين الذهب في روسيا
تعدين المطاحن الخام الصغيرة
عالية الكفاءة تعدين الذهب آلة الوالج معدات فاصل الذهب
rock crushing machinery panies
أرخص كسارة من الحصى للبيع في أتلانتا
تكلفة معدات تعدين رمال السيليكا
العمود المرفقي آلة طحن
فندق زينيث قريب
مهندسي التعدين في مصر
أسعار مصنع كسارة متنقلة
مطحنة مطحنة في تشيناي
تعدين صخور الفوسفات المتروكة في العالم
كسارة مطحنة الكوبالت الكرة
المستخدمة كسارة للبيع في ولاية البنجاب
vibration screen machine dalton japan
الفرق بين الأسطوانة محطم ، كسارة الفك
حول لدينا
تأسست شركة Henan Lrate للعلوم والتكنولوجيا المحدودة التي تصنع معدات التكسير والطحن الكبيرة والمتوسطة الحجم في عام 1987. وهي شركة مساهمة حديثة مع البحث والتصنيع والمبيعات معًا.
على مدار أكثر من 30 عامًا ، تلتزم شركتنا بنظام الإدارة العلمية الحديث والتصنيع الدقيق والريادة والابتكار. الآن أصبحت LIMING رائدة في صناعة تصنيع الآلات المحلية والخارجية.