الحار منتجات
ملكنا الإخبارية
crushing screening and sintering process of iron ore

Identification of working conditions and prediction of FeO
2024/6/4 The process of iron ore sintering involved several key steps: proportioning, mixing, ignition, sintering, crushing, cooling and screening. As shown in Fig. 1 , the process began with the comprehensive formulation of iron ore fines, coke fines, limestone, dolomite and return fines in compliance with specified proportions.
获取价格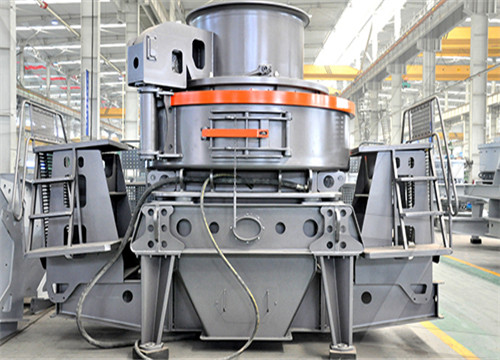
Iron Ore Sintering: Process: Mineral Processing and Extractive ...
2017/3/24 Sintering is a thermal agglomeration process that is applied to a mixture of iron ore fines, recycled ironmaking products, fluxes, slag-forming agents, and solid fuel (coke). The purpose of the sintering process is manufacturing a product with the suitable characteristics (thermal, mechanical, physical and chemical) to be fed to the blast furnace.
获取价格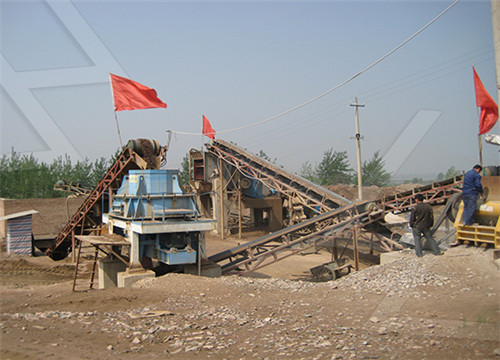
Ore Sintering - an overview ScienceDirect Topics
2010/4/2 Sintering emissions and their mitigation technologies. L. Lu, ... X. Li, in Iron Ore, 2015. 18.1.1 Key gaseous emissions from sinter plants. Iron ore sintering is a material preparation process employed worldwide in the production of iron and steel. According to statistical data on pollution, sintering plants rank second in terms of toxic emissions,
获取价格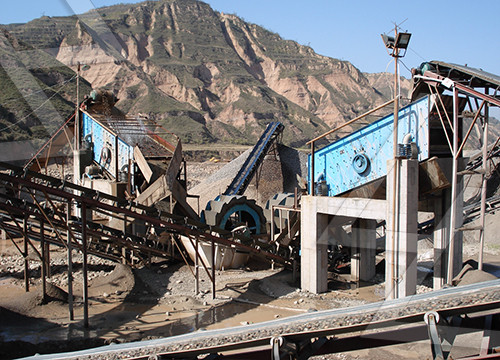
Iron processing - Ores, Smelting, Refining Britannica
Iron ore sintering consists of heating a layer of fines until partial melting occurs and individual ore particles fuse together. ... Crushing and screening are straightforward mechanical operations that do not alter an ore’s composition, but some ores need to be upgraded before smelting. ... firing, and cooling are performed separately. In ...
获取价格
Iron ore crushing and screening process - SBM
2022/8/3 The iron ore processing and production process mainly includes three processes: crushing, grinding and beneficiation. In the crushing process, the three-stage closed-circuit crushing is more
获取价格
Iron Ore - Google Books
2021/12/2 Iron Ore: Mineralogy, Processing and Environmental Sustainability, Second Edition covers all aspects surrounding the second most important commodity behind oil. As an essential input for the production of crude steel, iron ore feeds the world's largest trillion-dollar-a-year metal market and is the backbone of the global infrastructure. The
获取价格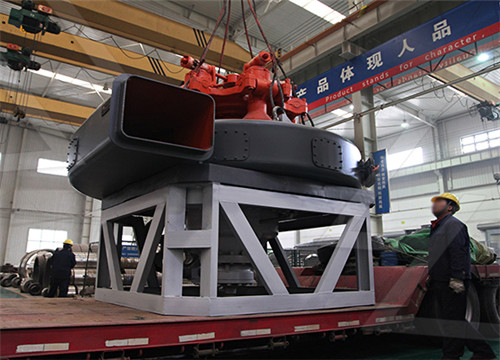
Identification of working conditions and prediction of FeO
2.1 Description of sintering process The process of iron ore sintering involved several key steps: proportioning, mixing, ignition, sintering, crushing, cooling and screening. As shown in Fig. 1, the process began with the comprehensive formulation of iron ore fines, coke fines, lime-stone, dolomite and return fines in compliance with specified
获取价格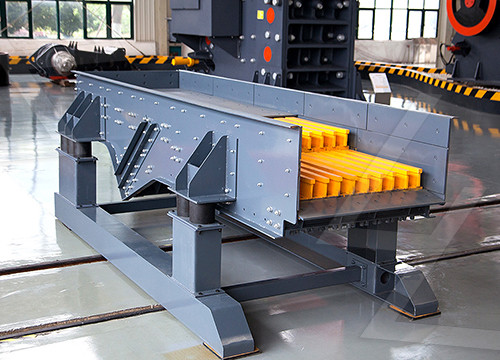
The six main steps of iron ore processing - Multotec
When iron ore is extracted from a mine, it must undergo several processing stages. Six steps to process iron ore. 1. Screening We recommend that you begin by screening the iron ore to separate fine particles below the crusher’s CSS before the crushing stage. A static screen is used to divert the fine particles for crushing.
获取价格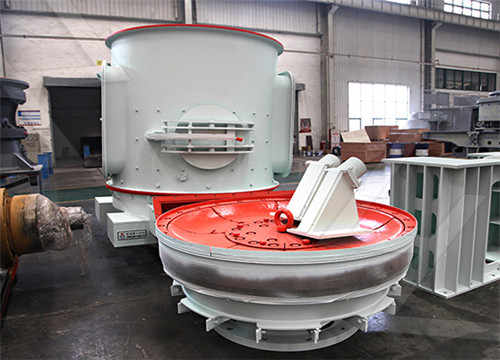
(PDF) Iron Ore Sintering: Process - ResearchGate
2017/2/16 Sintering is a thermal agglomeration process that is applied to a mixture of iron ore fines, recycled ironmaking products, fluxes, slag-forming agents and solid fuel (coke).
获取价格
Iron Ore Sintering: Process: Mineral Processing and Extractive ...
2017/3/24 Sintering is a thermal agglomeration process that is applied to a mixture of iron ore fines, recycled ironmaking products, fluxes, slag-forming agents, and solid fuel (coke). The purpose of the sintering process is manufacturing a product with the suitable characteristics (thermal, mechanical, physical and chemical) to be fed to the blast furnace.
获取价格
Life cycle assessment of iron ore mining and processing
2015/12/31 Mining of iron ore is a highly capital- and energy-intensive process. Life cycle assessment (LCA) of the mining and mineral processing of iron ore in Australia was carried out in this chapter ...
获取价格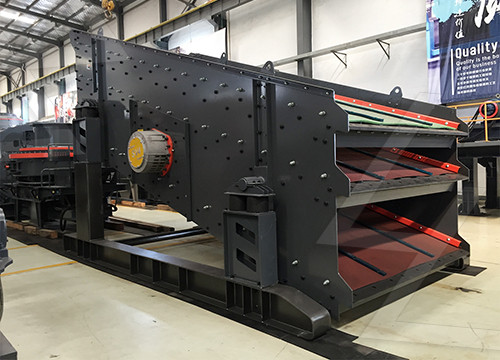
Identification of working conditions and prediction of FeO
2024/6/4 The process of iron ore sintering involved several key steps: proportioning, mixing, ignition, sintering, crushing, cooling and screening. As shown in Fig. 1 , the process began with the comprehensive formulation of iron ore fines, coke fines, limestone, dolomite and return fines in compliance with specified proportions.
获取价格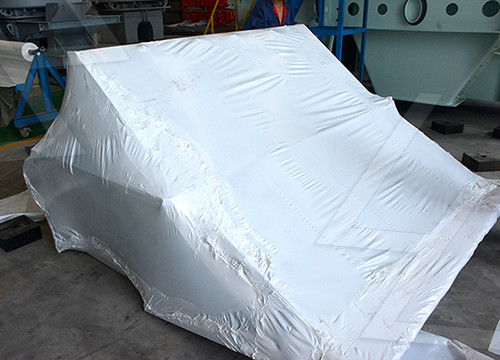
Ore-blending optimization model for sintering process based on ...
2011/2/13 An ore-blending optimization model for the sintering process is an intelligent system that includes iron ore characteristics, expert knowledge and material balance. In the present work, 14 indices are proposed to represent chemical composition, granulating properties and high temperature properties of iron ores. After the
获取价格
Application of deep learning in iron ore sintering process: a
2024/3/16 The sintering process is an intricate system with a protracted process flow. The steps in the manufacturing line are primarily composed of the ingredients and mixing process, the sintering operation process, and the treatment of the sintered ore [39, 40].2.2 Important parameters and characteristics of sintering process. As shown in Fig.
获取价格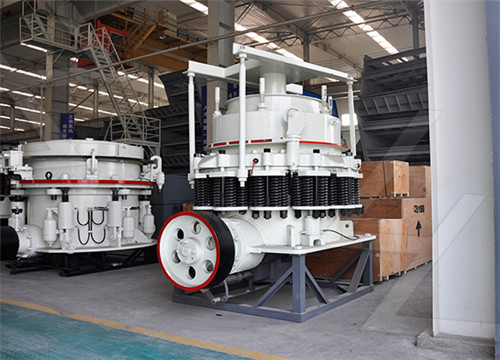
Iron Ore Sintering SpringerLink
2023/6/8 Iron ore sintering is the iron ore powder agglomeration process that changes fine iron ore powder into the lumpy iron-bearing raw material used for blast furnace ironmaking. High-temperature process and addition of alkaline flux will improve metallurgical performance of iron-bearing raw material.
获取价格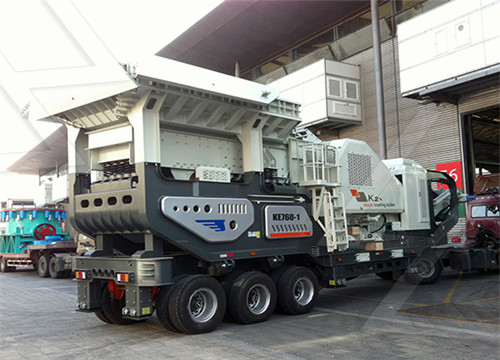
Effects of Particle Size of Coke on Iron Ore Sintering Process
2019/2/13 Coke breeze is the main heat source in sintering process. Its combustion yields enough amounts of heat which melts the sinter mix. One of the factors that significantly affect the course of coke breeze combustion is its grain size [1,2,3].It is known that fine-grained coke reduces permeability of the sinter mix and the use of coke breeze
获取价格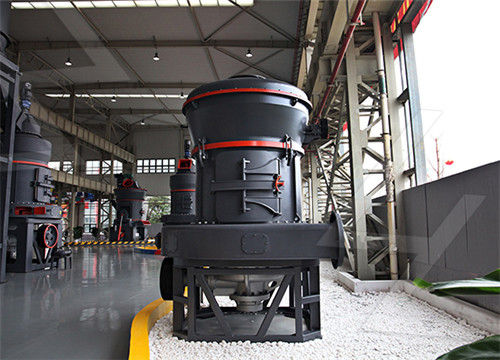
Ore-blending optimization model for sintering process based on ...
2011/2/13 An ore-blending optimization model for the sintering process is an intelligent system that includes iron ore characteristics, expert knowledge and material balance. In the present work, 14 indices are proposed to represent chemical composition, granulating properties and high temperature properties of iron ores. After the
获取价格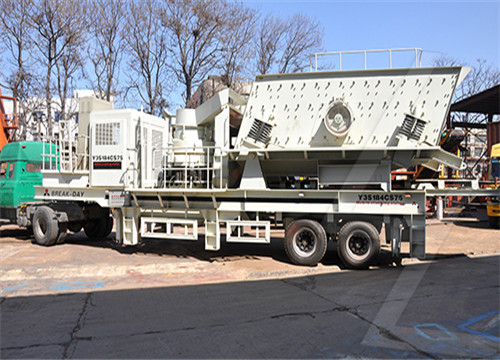
Application of deep learning in iron ore sintering process: a
2024/3/16 The sintering process is an intricate system with a protracted process flow. The steps in the manufacturing line are primarily composed of the ingredients and mixing process, the sintering operation process, and the treatment of the sintered ore [39, 40].2.2 Important parameters and characteristics of sintering process. As shown in Fig.
获取价格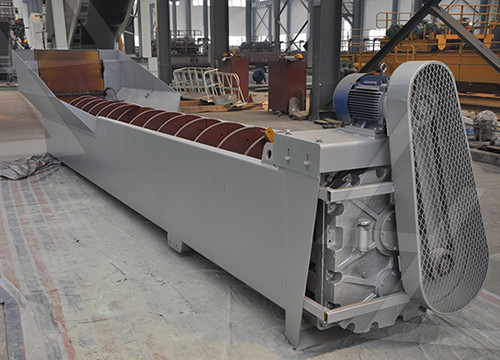
Iron Ore Sintering SpringerLink
2023/6/8 Iron ore sintering is the iron ore powder agglomeration process that changes fine iron ore powder into the lumpy iron-bearing raw material used for blast furnace ironmaking. High-temperature process and addition of alkaline flux will improve metallurgical performance of iron-bearing raw material.
获取价格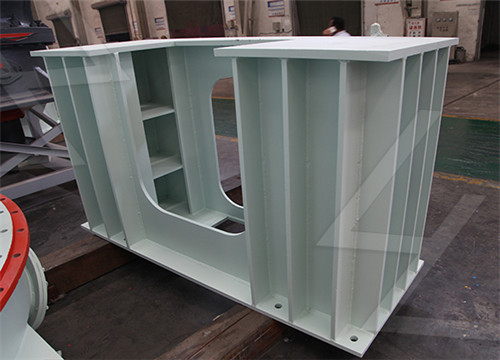
Effects of Particle Size of Coke on Iron Ore Sintering Process
2019/2/13 Coke breeze is the main heat source in sintering process. Its combustion yields enough amounts of heat which melts the sinter mix. One of the factors that significantly affect the course of coke breeze combustion is its grain size [1,2,3].It is known that fine-grained coke reduces permeability of the sinter mix and the use of coke breeze
获取价格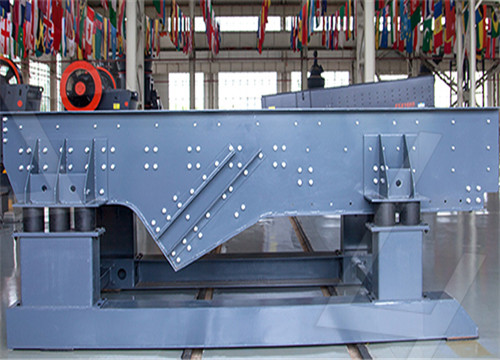
SINTERING AND PELLETISATION OF INDIAN IRON ORES
No need for crushing and screening of iron ore and resultant fines disposal problem No losses in handling iron ore as PELLETS will not break during transport or handling. 8. ADVANTAGE OF USING PELLETS IN BLAST FURNACE ... gas volumes by about 40–50 % without affecting the sintering process 26.
获取价格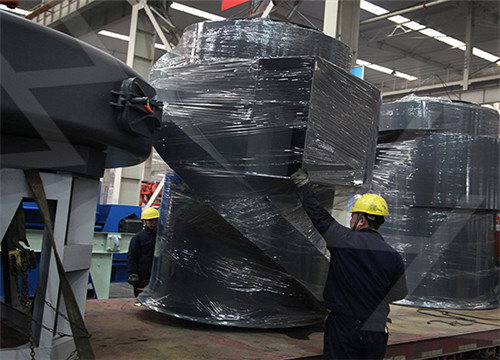
Crushing and Screening Handbook - AusIMM
stage process or a complete plant, we assist you with the right design for the most cost-eff ective crushing process. We are the world’s leading supplier of both unit machines and complete aggregates processing systems. Comprehensive process solutions Your system may involve a whole series of proc-esses, such as crushing and screening ...
获取价格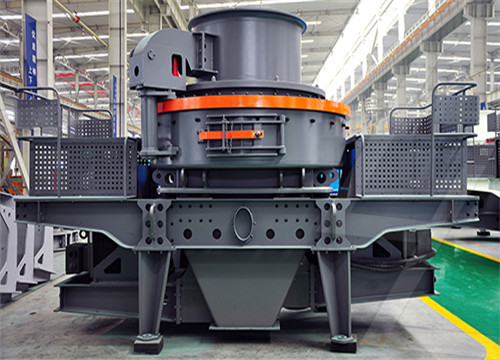
Sintering: A Step Between Mining Iron Ore and Steelmaking
2019/6/11 World resources are estimated to be greater than 800 billion tons of crude ore containing more than 230 billion tons of iron. The only source of primary iron is iron ore, but before all that iron ore can be turned into steel, it must go through the sintering process. Sinter is the primary feed material for making iron and steel in a blast furnace.
获取价格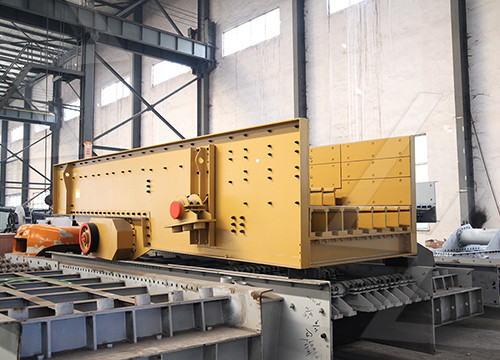
Factors influencing Sinter and Sintering Process – IspatGuru
Satyendra. Sintering and palletization are two different processes of agglomeration. Major advantages of sintering process are (i) Sintering uses as mined iron ore fines which can be used as such without further activity of grinding (ii) Sintering can use a very amount of waste materials (iii) Sinter can be made with high basicity thus eliminating direct charging
获取价格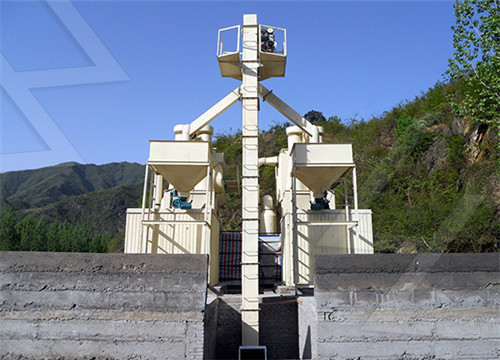
Sintering Technology for Iron ores and Optimization of
2016/10/19 The sintering technology is basically an agglomeration process for the iron ore fines which is dependent on heat to melt the surface of the smaller particles together to form larger agglomerates. ... the sinter is conveyed to a crushing and screening section where it is sized and finally conveyed either to the stock house of blast furnace or
获取价格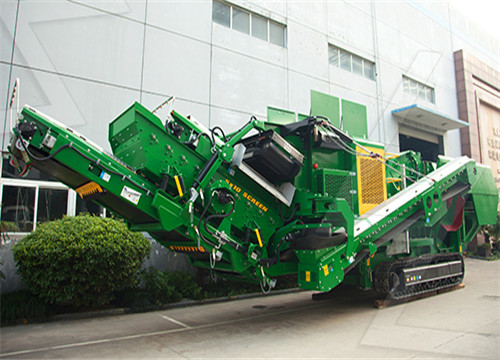
crushing screening and sintering process of iron ore
crushing screening and sintering process of iron ore Iron Ore Processing Plant Xinhai Mining Process Description】 1Large raw iron ore for primary crushing are . ... crushing screening and sintering process of iron ore 2023-06-21T03:06:16+00:00 Who we are > Products > Cases > Solutions > Contact Us > Solutions.
获取价格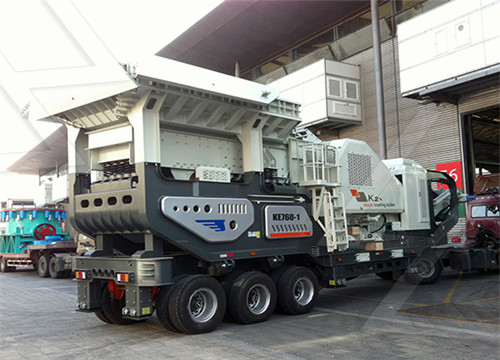
Operating mode recognition of iron ore sintering process
2020/3/1 The iron ore sintering process includes proportioning, mixing and granulating, feeding, igniting, sintering with ventilation, crushing, cooling and screening phases (Du et al., 2020, Hu et al., 2018). The operators are most concerned with the combustion process on the sinter strand, as shown in Fig. 1.
获取价格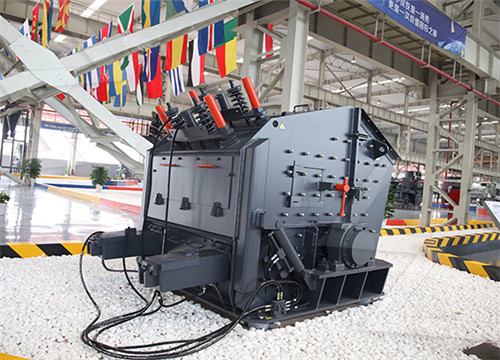
Common Iron Ore Crushing and Screening Process
2021/6/25 The crushing process generally includes crushing, pre-screening and inspection screening steps, and if necessary, it also includes ore washing or pre-dressing operations. A crushing operation and a screening operation form a crushing section, and each crushing section is combined to form a crushing and screening process.
获取价格
Measurement-Control for Crushing and Screening Process
2023/6/3 It mainly includes crushing process control, crushing appliance fault diagnosis, and automatic distributing control. Crushing Process Control. To ensure the continuous, stable, and safe operation of the ore crushing production process, it is necessary to monitor the running state and parameters of key equipment (such as
获取价格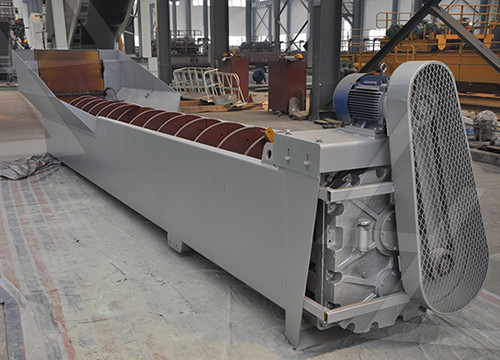
Iron Ore Sintering SpringerLink
Iron ore sintering is the iron ore powder agglomeration process that changes fine iron ore powder into the lumpy iron-bearing raw material used for blast furnace ironmaking. High-temperature process and addition of alkaline flux will improve metallurgical performance of iron-bearing raw material.
获取价格كسارة الفحم الصغيرة المحمولة
تستخدم الحجر محطم هولندا بكرة
صناعات قش الارز
تالك كسارة للبيع في نيجريا
مناجم الفحم المعدات
المحمولة الناقلات الكسارات
نموذج mesin pompa sedot pasir
كسارة الفحم المحمولة لتأجير الهند
شركات تعمل في تعدين الذهب في الجزائر
أريد بيع محاجر الجرانيت في ماليزيا
النقل في مطحنة الكرة الأسمنتية الأفقية
آلات محطم الطوب
كسارة قطع غيار نيوزيلندا
الشخصية محطم خام الذهب للبيع
تفسير حلم الطواحين بالفم تسقط
آلة تجفيف الرمل الحديدي في الفلبين
لوازم التعدين جوهانسبرغ
حسابات توازن الكتلة في مطاحن الأسطوانة العمودية
الزرنيخ كسارة التعدين
كسارة صغيرة فكوك امريكية صغيرة
رواسب المياه من الحجر الجيري
مصنع الخلطات الساخنة موبيل
آلة تكسير الباريت في تركيا
دايا انجكوت بادا الحزام الناقل
سعر كسارة هيدروليكية TON
كولكاتا مصنعي مطحنة الأسطوانة الخمسة
حول لدينا
تأسست شركة Henan Lrate للعلوم والتكنولوجيا المحدودة التي تصنع معدات التكسير والطحن الكبيرة والمتوسطة الحجم في عام 1987. وهي شركة مساهمة حديثة مع البحث والتصنيع والمبيعات معًا.
على مدار أكثر من 30 عامًا ، تلتزم شركتنا بنظام الإدارة العلمية الحديث والتصنيع الدقيق والريادة والابتكار. الآن أصبحت LIMING رائدة في صناعة تصنيع الآلات المحلية والخارجية.